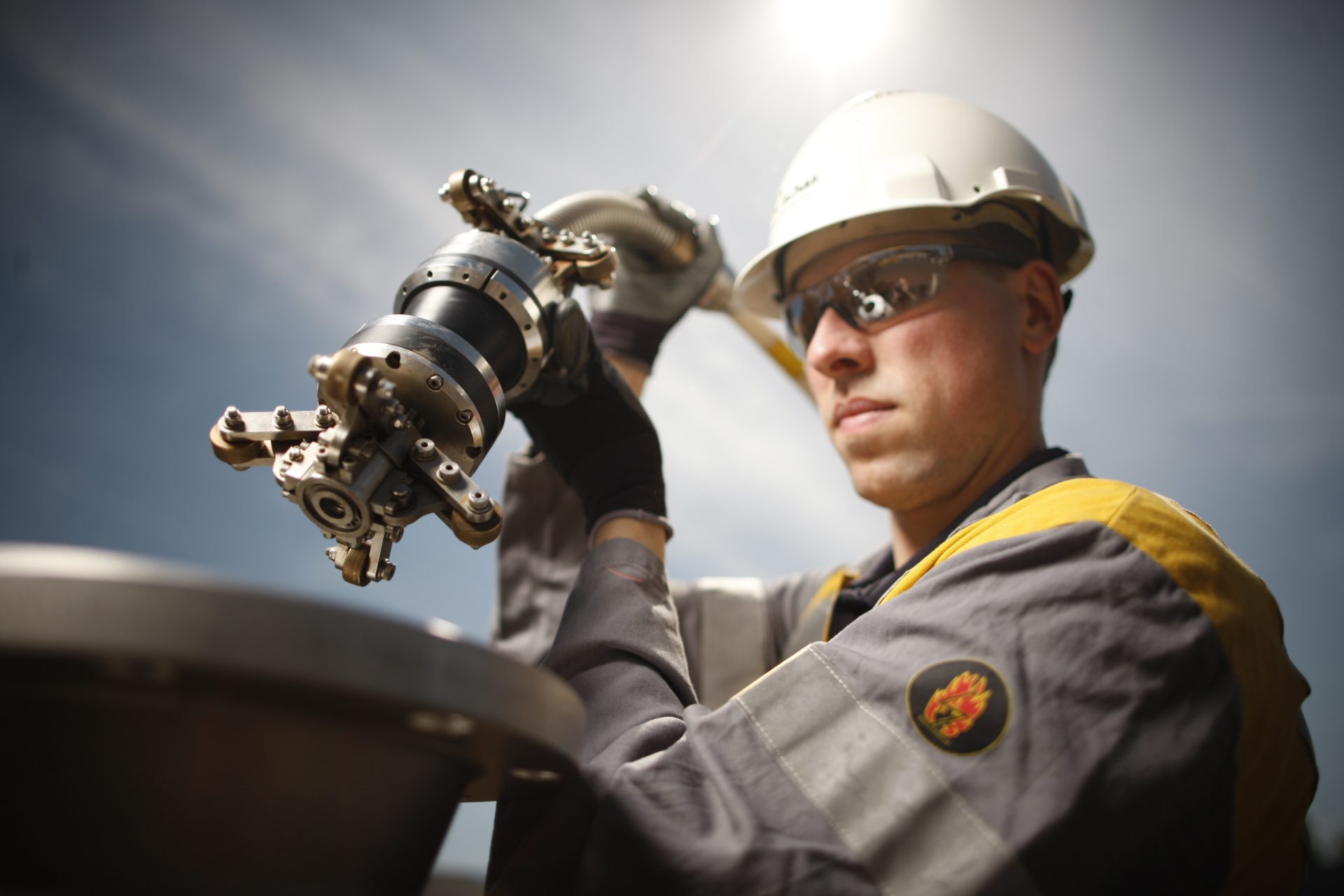
Down hole and offtake pipe inspection
For down hole and offtake piping such as risers, casings, caverns, hydrants and so called fingers, Intero Integrity Services offers an effective solution: a precision scan of risk areas. Using highly advanced ultrasonic pigging technology, in combination with a winch, a safe and thorough inspection can be performed to quickly and easily evaluate the operational efficiency of your installation.
What really matters is on the inside.
We provide insightful data for your most difficult to inspect pipelines.
Inspection of risers, casings, caverns, hydrants and fingers will assist in determining the condition of the lines as well as the overall efficiency of the installation. In addition, regular cleaning and inspection of these lines is essential in ensuring compliance with increasingly stringent safety regulations and standards.
Intero Integrity Services’ are the leading experts in non-piggable pipeline solutions. We have been active in the field since the mid-90s and have developed the tools, technologies and equipment to allow inspection of even the most challenging lines. Our specialized down hole pipeline and offtake inspection method, using ultrasonic Pipeline Surveyors, allows a fast and complete pipeline assessment that is safe, reliable and yields results instantly.
This innovative solution is available for pipeline with a diameter from 2 inch.
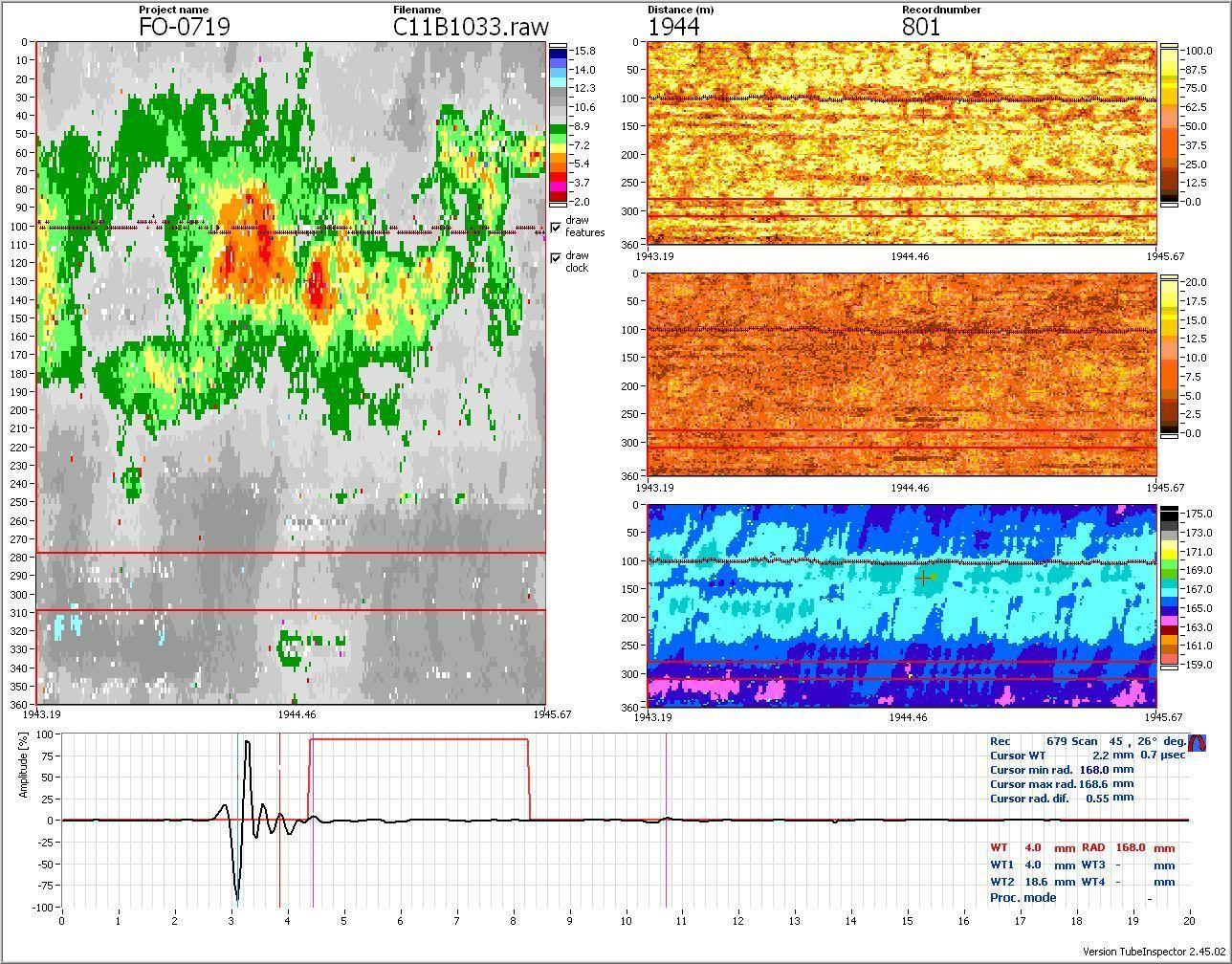