
Unpiggable MFL Robotic Inline Inspection
Advanced Pipe Explorer Robotics Technology Makes Every Pipeline Accessible
Self-propelled, remotely-controlled, and fully-articulated, Pipe Explorer goes where most cannot. With a minimal footprint, the ability to operate in active pipelines, and by collecting multipoint data in one pass, Pipe Explorer is the standard against which all others should be compared.
Our fleet of Pipe Explorer advanced robots are at the heart of the value we bring our customers. Fully-articulated and tetherless, Pipe Explorer provides comprehensive data that is comparable if not superior to more conventional pipeline inspection methods, enabling visual and non-destructive inspection with multipoint data collection of natural gas transmission and distribution pipelines as well as liquid terminals, facilities, and stations regardless of the difficulty of the location or complexity of the pipeline.
How MFL Robotic Inspections Work
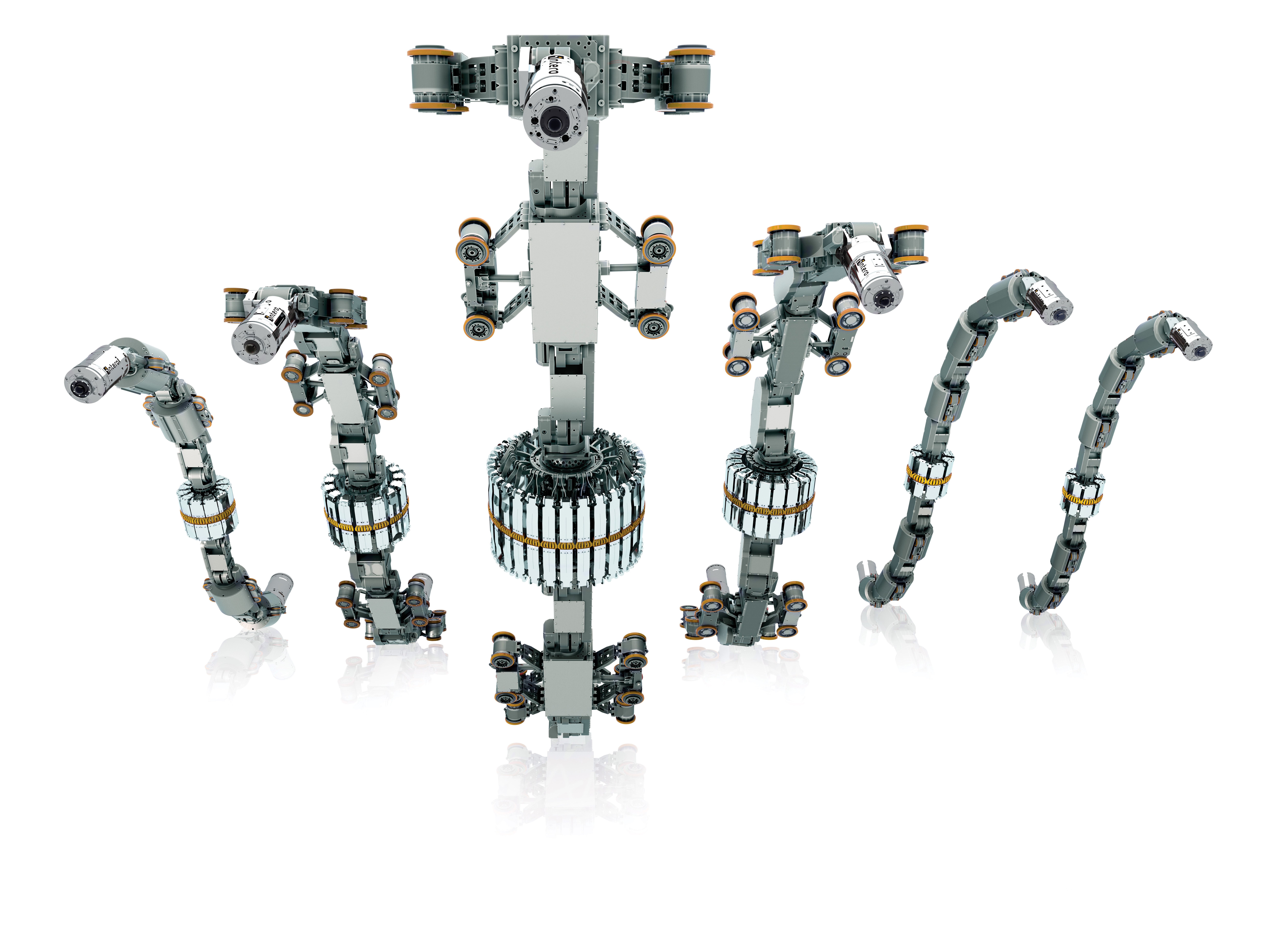
Throughout the inline inspection process, live video images of the pipeline and integrity data are streamed to both Intero and pipeline operators. These functions are performed without the need of a tether and without any interruption to local natural gas services. For liquid pipeline inspection, the pipes must be cleaned and emptied prior to inspection.
Step 1
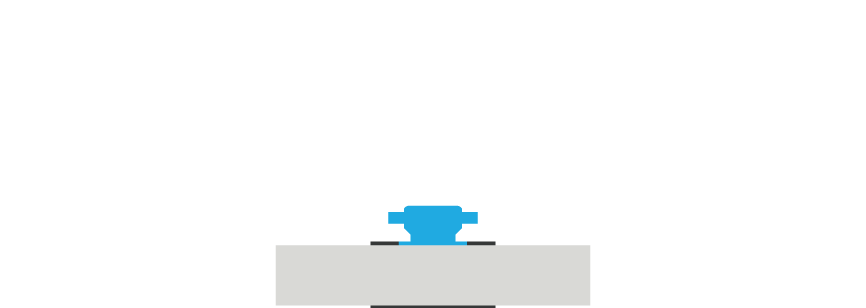
Pipeline operator welds a hot tap fitting to the pipeline.
Step 2
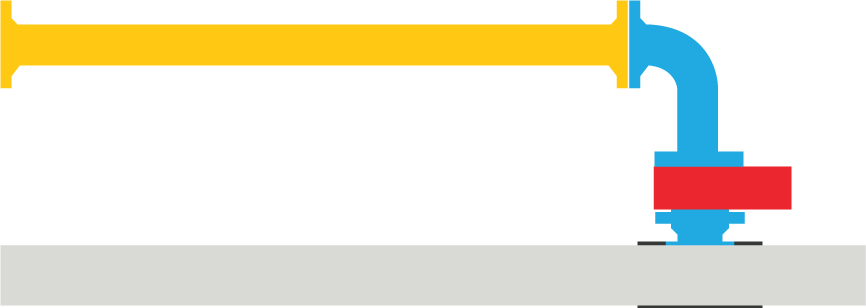
Pipe Explorer launch tube is secured to an industry-standard sandwich valve.
Step 3
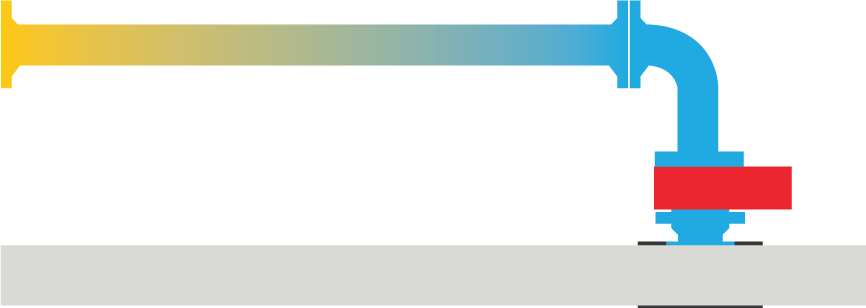
Intero operator launches Pipe Explorer into the pipeline, conducts the inspection, and retrieves the robot through the same hot tap (or a second hot tap if one is installed).

Unlock New Possibilities in Seam Weld Inspections
Innovation never stops. We’re expanding the capabilities of our robotic pipeline inspection technology to bring seam weld assessments to 10” and 12” pipes, building on our proven solutions for larger diameters.
The Benefits of Choosing Pipe Explorer for IN-Service Gas Pipeline Inspection
The Benefits of Choosing Pipe Explorer for OUT of Service Liquid Pipeline Inspection

Now Available - XYZ mapping
XYZ Mapping for Explorer 16/18, 20/26, and 30/36 is set to redefine unpiggable gas pipeline inspections.
Downloads & media
Papers
- Addressing Dents in Difficult-to-Inspect Natural Gas Pipelines: Enhancing Safety and Integrity with Robotics, Laser Technology, and Advanced Analytics1.37MBPDF
- Innovations in In-Service Robotic Inspection of Unpiggable Natural Gas Pipelines at River Crossing for which there are no Existing Launching and Receiving Capabilities720.89KBPDF
- Long Distance Inline Inspection of an Unpiggable Natural Gas Pipeline with Robotic Technology1.26MBPDF
